Table of Contents
Introduction
In the world of packaging, especially for products that are sensitive to oxygen and moisture, the semi – automatic vacuum nitrogen flushing seaming machine has emerged as a crucial piece of equipment. This machine combines the functions of vacuuming, nitrogen flushing, and seaming to ensure the long – term preservation of various products. Let’s delve into all aspects of this remarkable machine.
How It Works
Vacuuming
The first step in the process is vacuuming. The machine creates a low – pressure environment inside the can or container. A powerful vacuum pump is used to remove the air, including oxygen, from the package. Oxygen is a major culprit in food spoilage, as it can cause oxidation, mold growth, and the deterioration of flavors and nutrients. By removing oxygen, the shelf – life of the product is significantly extended.
Nitrogen Flushing
After the vacuuming process, nitrogen gas is introduced into the container. Nitrogen is an inert gas, which means it does not react with the product inside. It replaces the removed oxygen, creating a protective atmosphere. Nitrogen flushing helps to further prevent oxidation, maintain the product’s freshness, and protect it from external contaminants.
Seaming
Once the container is filled with nitrogen, the seaming process begins. The machine uses a set of seaming rollers to tightly seal the lid onto the can or container. A proper seam is essential to maintain the integrity of the vacuum and nitrogen environment inside the package, ensuring that no air or moisture can enter.
Key Features
Semi – Automatic Operation
As the name suggests, this machine is semi – automatic. It requires some manual intervention, such as placing the cans or containers on the seaming station and removing the sealed products. However, the vacuuming, nitrogen flushing, and seaming processes are automated. This combination of manual and automated functions makes the machine suitable for small to medium – scale production, where flexibility and cost – effectiveness are important.
Adjustable Parameters
The semi – automatic vacuum nitrogen flushing seaming machine allows operators to adjust various parameters according to the specific requirements of the product. For example, the vacuum level can be adjusted to ensure that the right amount of air is removed from the container. The nitrogen flushing time and flow rate can also be customized to achieve the optimal nitrogen concentration inside the package. Additionally, the seaming pressure and speed can be set to create a secure and consistent seal.
Compatibility with Different Containers
This machine can be used with a wide range of containers, including cans, jars, and bottles. It can handle different sizes and shapes of containers, making it a versatile choice for various industries. Whether you are packaging food products, pharmaceuticals, or chemicals, the semi – automatic vacuum nitrogen flushing seaming machine can meet your needs.
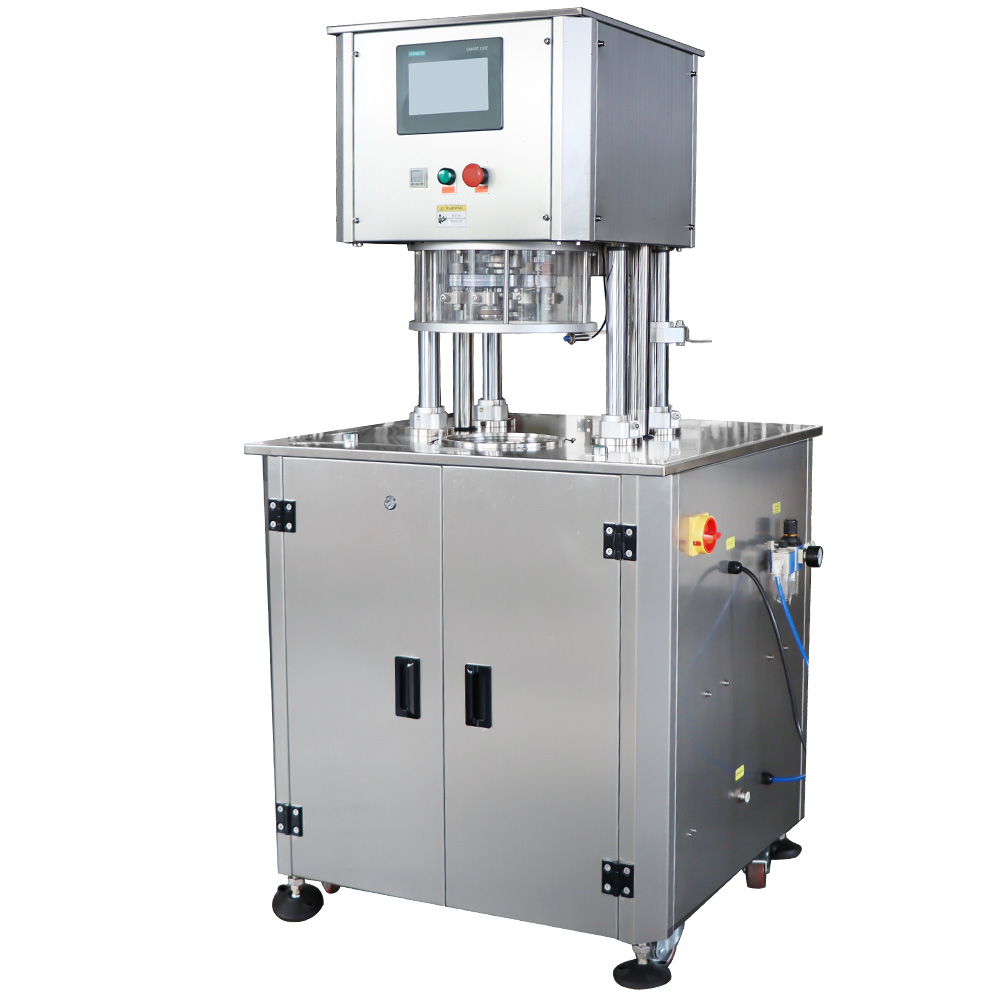
Advantages
Extended Shelf – Life
By removing oxygen and replacing it with nitrogen, the machine significantly extends the shelf – life of the products. This is especially important for perishable items such as food, beverages, and certain pharmaceuticals. Longer shelf – lives reduce waste and allow manufacturers to distribute their products over a wider geographical area.
Preservation of Product Quality
The protective nitrogen atmosphere helps to preserve the color, flavor, texture, and nutritional value of the products. For example, in the food industry, nitrogen flushing can prevent the browning of fruits and vegetables, the staling of baked goods, and the rancidity of oils. This ensures that the products reach the consumers in the best possible condition.
Cost – Effective
Compared to fully automatic machines, semi – automatic vacuum nitrogen flushing seaming machines are more affordable. They require less initial investment and are suitable for businesses with limited production volumes. Additionally, the adjustable parameters allow for efficient use of nitrogen and energy, further reducing operating costs.
Maintenance and Safety
Maintenance
Regular maintenance is essential to keep the semi – automatic vacuum nitrogen flushing seaming machine in good working condition. This includes cleaning the machine, checking the vacuum pump and nitrogen supply system for leaks, and lubricating the moving parts. It is also important to replace worn – out components such as seaming rollers and gaskets in a timely manner.
Safety
Safety is a top priority when operating this machine. Operators should be trained on how to use the machine safely, including how to handle the vacuum and nitrogen systems. The machine should be equipped with safety features such as emergency stop buttons and safety guards to prevent accidents. Additionally, proper ventilation is required to ensure that any leaked nitrogen or other gases are safely removed from the working area.
Conclusion
The semi – automatic vacuum nitrogen flushing seaming machine is a valuable tool for businesses looking to improve the quality and shelf – life of their products. Its combination of vacuuming, nitrogen flushing, and seaming functions, along with its adjustable parameters and compatibility with different containers, make it a versatile and cost – effective solution. By understanding how the machine works, its key features, advantages, and maintenance requirements, manufacturers can make the most of this technology and enhance their packaging processes.