In the world of product packaging, especially for items stored in glass bottles, maintaining freshness and quality is of utmost importance. Automatic glass bottle vacuum capping machines play a pivotal role in achieving these goals, and here’s how.
Table of Contents
Creating a Vacuum Environment
The first and most crucial step in the process is the creation of a vacuum inside the glass bottle. When a product is filled into a bottle, there is often air present. This air contains oxygen, which can have detrimental effects on the product. For food items, oxygen can cause oxidation, leading to changes in flavor, color, and nutritional value. In the case of beverages, it can cause carbonation loss or spoilage.
Automatic glass bottle vacuum capping machines use powerful vacuum pumps to remove the air from the bottle. Once the air is evacuated, the level of oxygen inside the bottle is significantly reduced. This creates an environment where the product is protected from the harmful effects of oxidation. For example, in the wine industry, a proper vacuum seal can prevent the wine from turning into vinegar by minimizing the contact of the wine with oxygen.
Ensuring a Tight Seal
After the vacuum is created, the machine proceeds to cap the bottle. A tight seal is essential for maintaining the vacuum and preventing any outside air or contaminants from entering the bottle. These machines are designed with precision mechanisms that ensure the cap is applied evenly and firmly onto the bottle neck.
The capping process involves applying the right amount of pressure. Too little pressure, and the seal may not be tight enough, allowing air to seep in over time. Too much pressure, on the other hand, could damage the bottle or the cap. Automatic glass bottle vacuum capping machines are calibrated to apply the optimal pressure for each specific bottle and cap combination. This results in a hermetic seal that keeps the product fresh and protected.
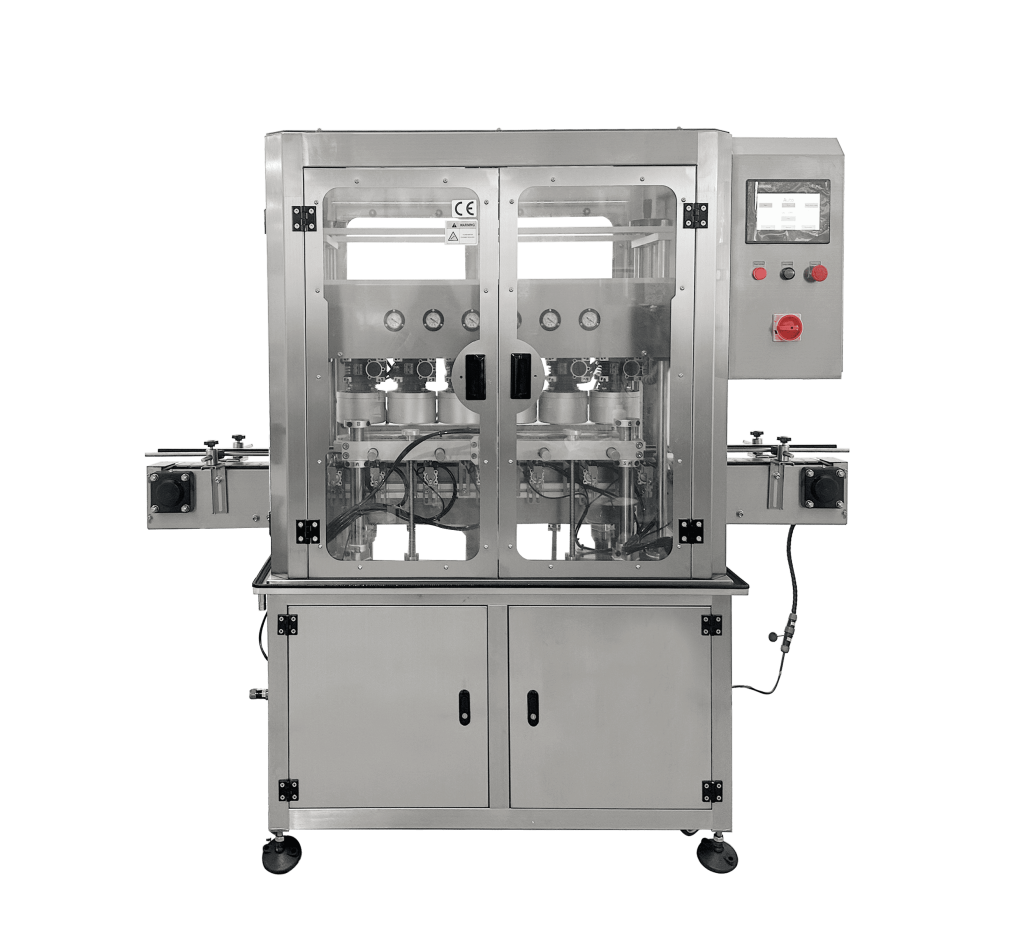
Consistent Quality Control
One of the significant advantages of using automatic machines is the ability to maintain consistent quality. These machines are programmed to perform the same sequence of operations with high precision for every single bottle. This means that each bottle receives the same level of vacuum and the same quality of capping.
In a manual capping process, there is a higher chance of human error. Different operators may apply different levels of pressure or may not create a proper vacuum every time. With automatic glass bottle vacuum capping machines, this variability is eliminated. As a result, consumers can expect the same level of freshness and quality in every bottle they purchase.
Hygiene and Contamination Prevention
Automatic glass bottle vacuum capping machines are designed with hygiene in mind. They are often made of materials that are easy to clean and sanitize. The automated process reduces the need for human contact with the product during the capping stage, minimizing the risk of contamination.
In industries such as food and pharmaceuticals, where strict hygiene standards must be met, these machines are invaluable. They prevent the introduction of bacteria, dust, and other contaminants into the bottle, ensuring that the product remains safe and of high quality throughout its shelf – life.
Adaptability to Different Products
These machines are highly adaptable and can be used for a wide range of products. Whether it’s a thick sauce, a delicate perfume, or a liquid medication, the automatic glass bottle vacuum capping machine can be adjusted to handle different viscosities and bottle sizes. This versatility allows manufacturers to use the same machine for multiple product lines, streamlining their production processes while still ensuring the freshness and quality of each product.
In conclusion, automatic glass bottle vacuum capping machines are essential tools for any industry that uses glass bottles for packaging. By creating a vacuum, ensuring a tight seal, maintaining consistent quality, preventing contamination, and adapting to different products, these machines go a long way in ensuring that the products reach consumers in the best possible condition, fresh and of high quality.